稼働率は工場の生産性を上げるうえで重要な考え方です。
しかし稼働率の理解には数学的な思考が必要なため、理解しにくい部分もあるでしょう。
そこでこの記事では、稼働率とは何かや稼働率の求め方、稼働率と可動率の違いなどについて詳しく解説します。
設備総合効率や性能稼働率、時間稼働率など踏み込んだ内容にも触れているので、稼働率に対する知識を深めたい人はぜひ参考にしてください。
この記事を書いた人:受発注ライフ編集部
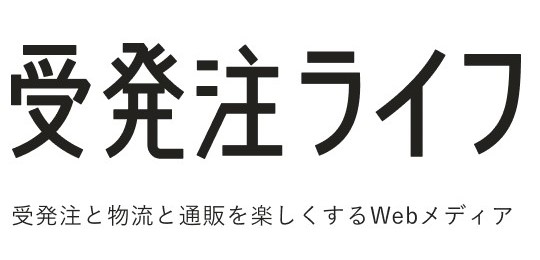
『受発注ライフ』は、2024年3月22日に誕生した、株式会社カンナートのWebメディアです。
株式会社カンナートは西新宿にある創業20年目のシステム開発会社です。
このメディアでは、受発注業務や物流、通販にお困りごとのある方々に向けて、 業務改善のアイデアや業界の新しい動向などを発信していきます。
稼働率と可動率の違い
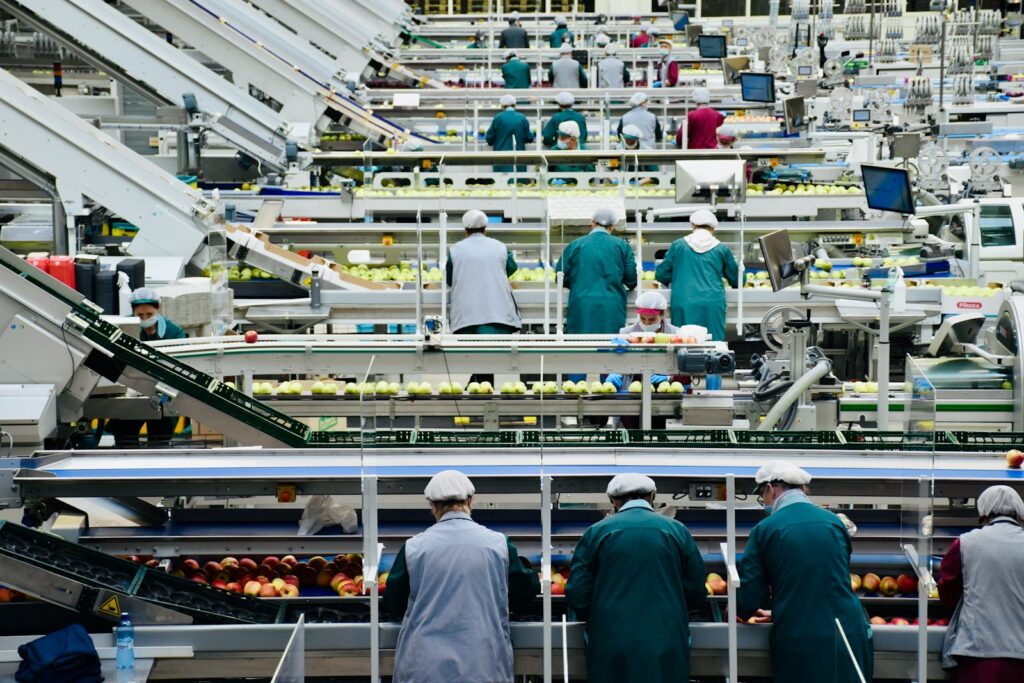
ここでは稼働率と可動率の違いを紹介します。
また可動率と稼働率の計算方法や例題も載せているので、参考にしてください。
稼働率とは
工場・設備における稼働率とは、生産できる数に対しての実際に生産している数の割合を意味します。
稼働率を上げるためには、工場のオペレーションなどを工夫することが重要です。
しかしオーダーや需要がなければそもそも生産自体ができないため、その場合稼働率は0%となります。
稼働率の計算方法については、この後詳しく解説します。
稼働率の計算方法
稼働率の計算式は以下の通りです。
稼働率=実際に生産された量÷通常生産できる量(生産能力)
ここでは一つ、稼働率の求め方の例題を紹介します。
ある工場では、1日当たりの生産能力は100個、それに対し実際に生産した数は70個あったとします。
この場合稼働率の求め方は、70÷100=70%となります。
同工場で130個実際に生産した場合、稼働率は130%です。
可動率とは
可動率とは設備を動かす必要がある時、実際に動いたかを表わす割合です。
仮に、設備を動かしたい時に100%の確率で機械が動いたとすると、可動率は100%。
一方、設備トラブルなどで機械が動かない時間が増えると、可動率は低くなります。
稼働率と可動率の違いは、稼働率はオーダー数に左右されるのに対して可動率は左右されないこと。
ですがどちらの指標も、生産性を向上する目的で活用される点で共通しています。
可動率の計算方法
可動率の計算式は、以下の通りです。
可動率=(総運転時間-停止時間)÷総運転時間
例えば工場の生産ラインで、1日の運転予定時間は8時間あり、途中で機械故障により2時間停止したとします。
この場合、上記の式が表わす総運転時間は8時間、停止時間は2時間です。
これを式に当てはめると、(8-2)÷8の=可動率は75%。
この結果から、総運転時間のうち25%の時間、機械は停止していたことが分かります。
設備総合効率(OEE)とは
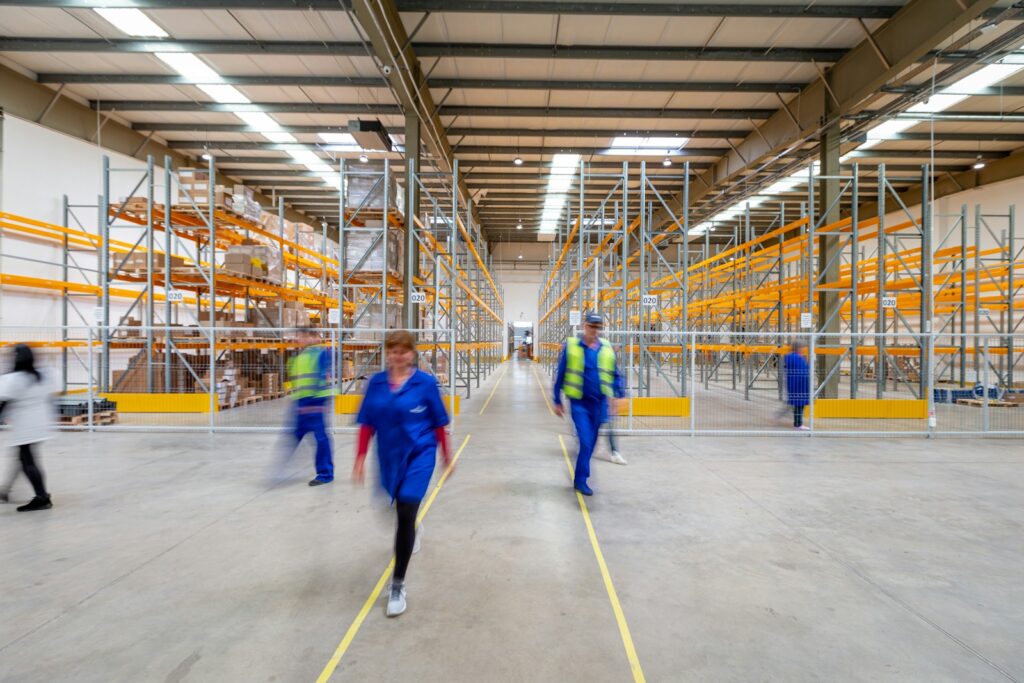
設備総合効率(OEE)とは、生産効率の向上を目的に活用される指標です。
ここでは設備総合効率の3要素である、性能稼働率、時間稼働率、良品率3つの概念について解説します。
性能稼働率
性能稼働率は設備総合効率の一つで、設備が稼働した時間の中で、性能通り設備が稼働した時間の割合です。
この「性能通り」とは、機械が不具合なく正常に動いている状態の意味。
性能稼働率は、基準サイクルタイム×加工数量÷稼働時間、もしくは正味稼働時間÷稼働時間で算出できます。
性能稼働率が低くなる原因には、チョコ停や空運転があります。
時間稼働率
設備総合率の二つ目、時間稼働率とは負荷時間のうち実際に設備を稼働した時間のこと。
負荷時間とは実際に設備に電源が入っていて、稼働可能な時間のこと。
時間稼働率が低下する原因は、機械の故障や生産ラインを切り替える時の段取りの悪さ、設備の工具交換などさまざまです。
最近では人工知能による予知保全システムを活用することで、故障のリスクを未然に察知し時間稼働率を上げる企業も増えています。
良品率
良品率とは生産した数量に対し、どの程度良品が存在するか表した指標です。
良品率の計算方法は、(加工数量-不良数量)÷加工数量。
良品率は100%が理想的で、それを目指すためには最終検査の徹底や機械のメンテナンスなどの対策が必要です。
また生産工程の自動化や、人口知能による生産設備の監視も良品率向上につながります。
稼働率の目安
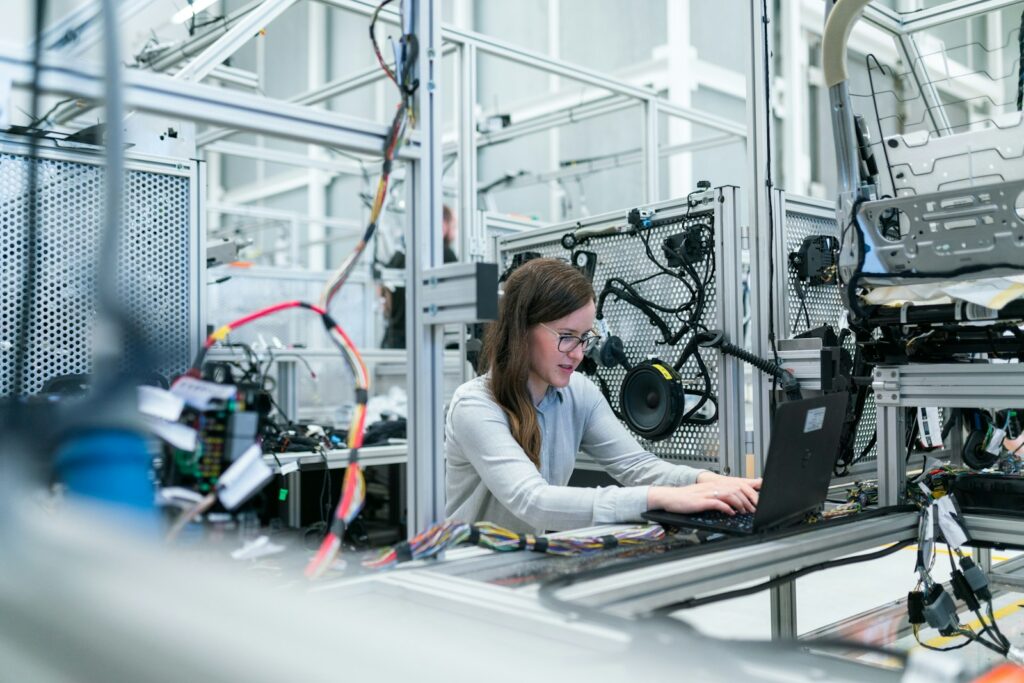
稼働率は100%が理想的ですが、これを大きく下回ることもあれば上回ることもあります。
ここでは稼働率の目安について解説します。
稼働率が低い時
稼働率が50%を下回る場合、設備が実際に稼働している時間が設備全体における生産可能時間より少ない状態です。
また、設備生産能力と比べ受注を受けた量が少ない際にも稼働率は下がります。
稼働率の数値が低い状態では、一般的に生産活動を効率的に実施できません。
稼働率が高い時
稼働率は100%となるのが理想的。
この状態は生産活動が効率的に進んでいることを表わしています。
100%とは行かなくとも、できるだけ高い稼働率を目指すことで生産性は向上するでしょう。
稼働率を上げるためには、前述した性能稼働率、時間稼働率などの設備総合効率向上に向けた努力が必要です。
稼働率が100%を超える時
稼働率が100%を超える場合、要注意です。
稼働率が100%を超えるということは、生産設備が本来持つ生産能力を超えていることを意味します。
またこの状況が長期化すると、従業員に過大な負荷がかかったり機械が故障したりする可能性もあるので注意しましょう。
稼働率や可動率が低下する原因
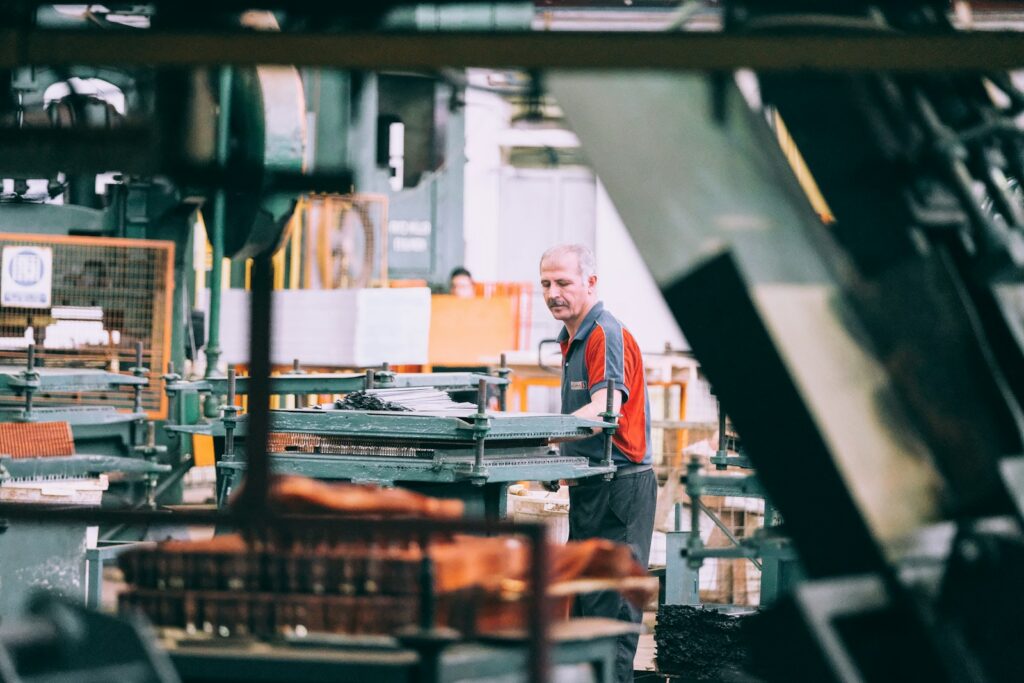
稼働率や可動率が低下する原因を理解しておくことで、低下を未然に防ぐことが可能です。
低下する原因は、主に以下4つです。
設備の故障(ドカ停)
設備の故障によるドカ停が生じると、稼働率や可動率が大きく低下します。
ドカ停とは、トラブルが生じてから操業を再開するまでに1時間を超えてしまうようなトラブルのことです。
ドカ停が一度生じると大きな損失に繋がり、場合によっては経営を左右するような大問題に発展することも。
チョコ停
チョコ停とは製造業で使われる専門用語で、製造設備が少しの時間停止するトラブルのことです。
例えば、部品が詰まったなどすぐに解決できる些細なトラブルをチョコ停といいます。
少しの時間であっても、回数が増えれば増えるほどロスが大きくなるため注意が必要です。
段取り替え
段取り替えとは製造する部品や製品を切り替えるタイミングで発生する、設備の設定変更の作業です。
段取り替え中は生産ラインや機械を停止しなければならないため、できるだけ段取り替えが少なくて済むスケジュールにすることがポイントです。
不良品が多い
不良品が発生してしまうと、その数だけ製品を追加生産しなければならないため生産効率が低下してしまいます。
例えば本来100個生産しようと思っていた製品に不良品が10個あった場合、新たに10個製造する必要があるため、その分の時間が全体の稼働率を低下させます。
稼働率や可動率を100%に近づける方法
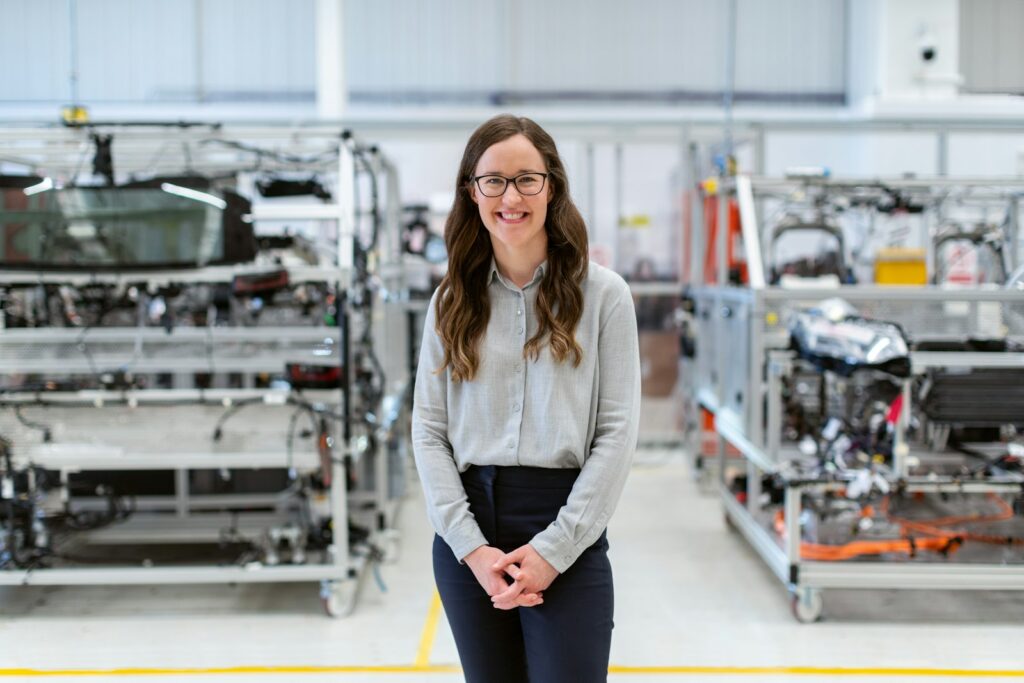
稼働率や可動率を100%に近づけることが、製造業でより効率的に利益を獲得するポイントです。
ここでは、稼働率や可動率を100%に近づける方法を紹介します。
設備のメンテナンスを定期的に行う
設備の不具合やトラブルは、稼働率と可動率ともに下げてしまいます。
設備のトラブルが発生する代表的な原因が、長期間設備を使ったことで起こる劣化や老朽化です。
稼働率と可動率を高めるには、メンテナンスを定期的に行いエラーや故障を防止することが大切です。
段取り替えを効率化する
段取り替えによる設備の停止時間を短くすることで、稼働率と可動率ともに向上できます。
同じラインで複数の部品や製品を作っている場合には、段取り替えを効率化できないか検討しましょう。
作業手順を見直したり、複数人で協力して段取り替えを行ったりすることで、段取り替えのスピードは上がります。
ボトルネック特定
ボトルネックとは、業務の生産性低下を招いている工程や設備、人などの要素を指します。
ボトルネックを洗い出し、それに対する解決策を検討、実践することで稼働率や可動率を上げることが可能です。
ボトルネックを探す際には、IoTの活用が有効です。
製造工程の自動化
製造工程の自動化で、人の作業が原因のトラブルや生産効率の低下が防げます。
例えばロボットアームや自動搬送装置を設備に導入すれば、作業員にかかる負担も減らせ結果的に稼働時間を増やすことが可能。
またロボットは24時間稼働できるため、生産効率が向上します。
まとめ
今回は稼働率とは何かや稼働率と可動率の違い、稼働率の計算方法などについて解説しました。
稼働率の求め方や目安を知っておくことは、工場の生産性を考えるうえで重要なことです。
稼働率を上げるため、時間稼働率や性能稼働率、良品率などの設備総合効率を一つ一つ改善してみてください。
設備のメンテナンス、段取り替えの効率化など小さな努力の積み重ねが、稼働率を徐々に高めていくでしょう。