人が携わる作業に、ポカミスは付き物。
完全に無くすことは難しいですが、適切な対策を講じることでできるだけ減らしたいものです。
この記事ではポカミスの定義や言い換えから原因、事例、防止策などについて詳しく解説します。
ポカミスを減らすことは、作業の質を高めるだけでなく作業効率アップにも繋がります。
仕事のポカミスへの対策を知りたい人はぜひ参考にしてください。
この記事を書いた人:受発注ライフ編集部
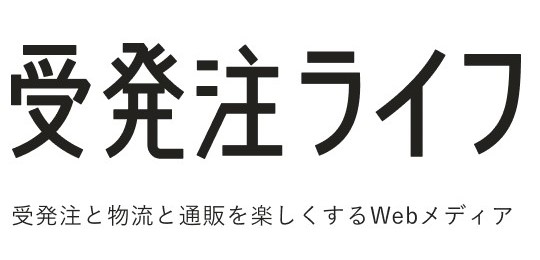
『受発注ライフ』は、2024年3月22日に誕生した、株式会社カンナートのWebメディアです。
株式会社カンナートは西新宿にある創業20年目のシステム開発会社です。
このメディアでは、受発注業務や物流、通販にお困りごとのある方々に向けて、 業務改善のアイデアや業界の新しい動向などを発信していきます。
ポカミスの定義とは?
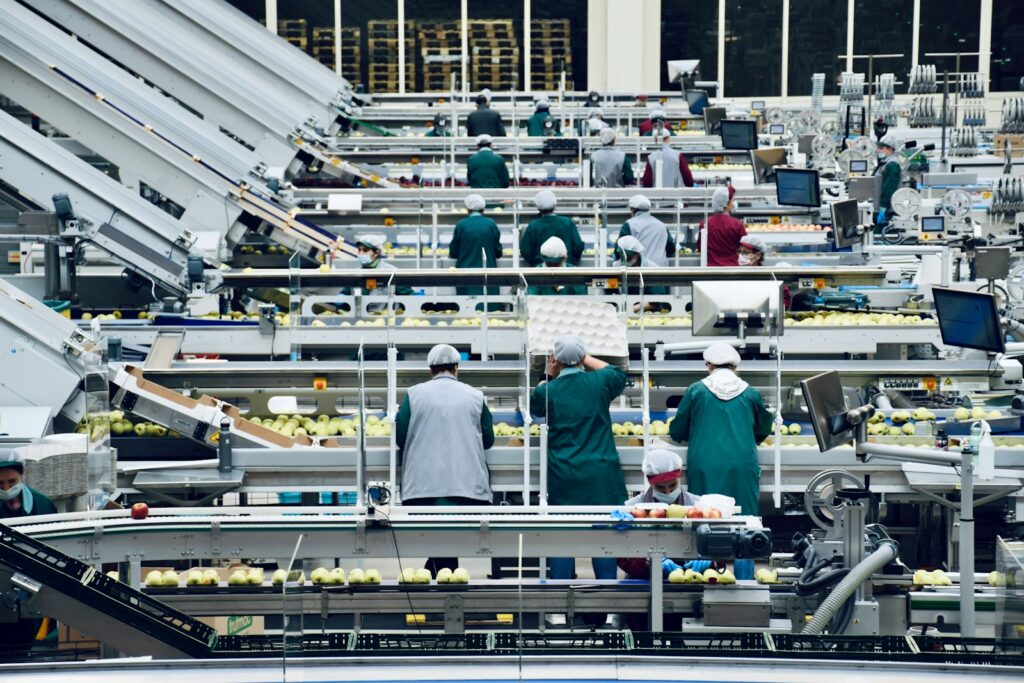
ポカミスとは注意不足から生じるミスと定義され、ケアレスミスや凡ミスとも言い換えられることがあります。
もともとは製造業で使われていた業界用語でしたが、現在では日常生活で使われることも。
例えば書類の誤記入や物の置き忘れなどは、日常生活における典型的なポカミスの事例。
ポカミスは誰にでも起こりうるため、発生した際には冷静に対処し再発防止に努めることが大切です。
ポカミスが発生する原因
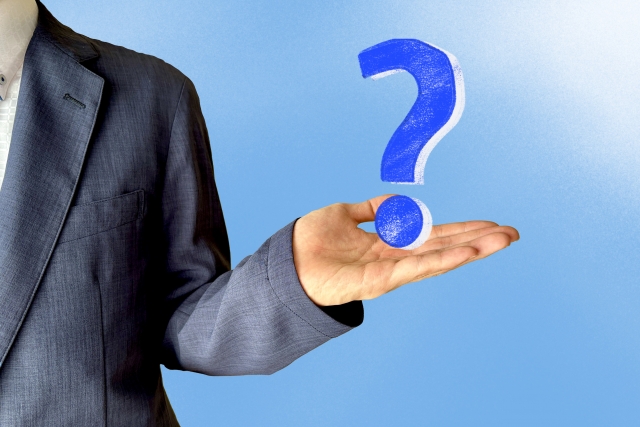
ポカミスが生じる原因には、ヒューマンエラーによるものが多いです。
また作業環境の問題や教育体制の不備など、雇用主側の原因でポカミスが生じることもあります。
ヒューマンエラー
日本工業規格によると、ヒューマンエラーとは「意図しない結果を生じる人間の行為」と定義されています。
ヒューマンエラーはポカミスの主要な原因の一つで、注意力の散漫や判断ミス、思い込みによることがほとんど。
うっかりが原因であることや、怠慢が原因のケース、そのどちらも合わさったケースもあります。
製造業では、ヒューマンエラーにより製品不良や誤出荷などの重大な問題が生じえます。
作業環境に問題がある
作業環境の問題も、ポカミスの発生に大きく影響します。
例えば不適切な照明や温度管理、騒音は、作業者の集中力を低下させ、ミスを引き起こす可能性があるでしょう。
また整理整頓されていない作業スペースでは必要な道具や情報を見つけるのに時間がかかり、効率性を損なうことになります。
作業環境の問題は作業員の怪我の一因になることもあるため、企業が率先して取り組むべき課題です。
ルール・教育体制の不備
ポカミスはしばしばルールや教育体制の不備が原因で発生します。
例えば複雑な業務にも関わらずマニュアルが無い、研修が不十分などの状況ではポカミスが多発するでしょう。
またマニュアルやルールが古いまま改定されていないと、作業手順のミス、機械の誤操作などのミスが生じます。
特に作業に不慣れな新人はポカミスを引き起こしやすいため、教育担当を設けるなどしてミスを事前にカバーする仕組みを作ることが不可欠です。
製造業におけるポカミスの事例
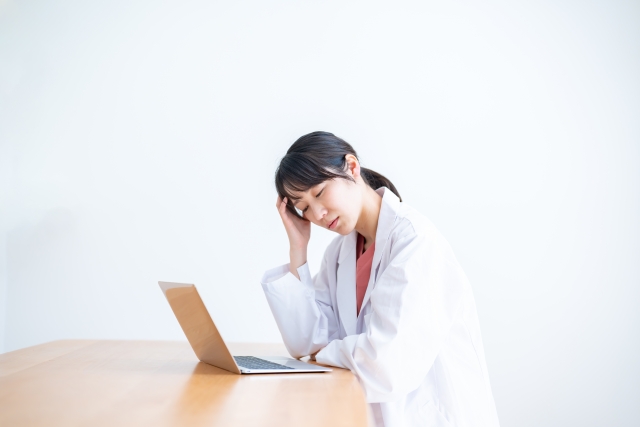
製造業における典型的なポカミスの事例は、不良品増加、怪我、出荷ミス・遅延の3つです。
ポカミスを放置すると、企業の信用低下などの深刻な問題に繋がります。
不良品の増加
製造業におけるポカミスは、不良品の増加を引き起こす可能性があります。
例えば作業員が勘違いで部品を取り付ける位置を間違えたり、注意力不足でパッケージを傷付けてしまったりするのはポカミスの典型的な事例です。
不良品が増加するとその分の商品を新たに作り直さなければならないので、企業にとって大きな経済的な損失となります。
作業員の怪我
ポカミスにより作業員が怪我を負うといった事例は、製造業でしばしば見られます。
そのような事例の中には、機械に手が挟まり指を切断する、危険物が目に入り失明するなど重大事故も少なくありません。
また安全器具の装着をうっかり忘れるなど、重大なポカミスをした場合には命を落とすことも。
ポカミスによる怪我は慣れや過信から生じるケースも多く、ベテラン社員も気を付けなければなりません。
出荷ミス・遅延
製造業におけるポカミスは、出荷ミスや遅延の原因となることもあります。
例えば在庫が切れているのに発注をうっかり忘れたり、納品数を間違えたりすると、生産が滞り出荷遅延に繋がります。
また宅配伝票を書き間違えるなどの凡ミスをすれば、スケジュール通りに出荷しても購入者のもとに商品が届きません。
出荷ミスや遅延は、顧客満足度の低下、信頼性の損失、そして最終的には売上げの減少に直結します。
ポカミスを防止するための手順
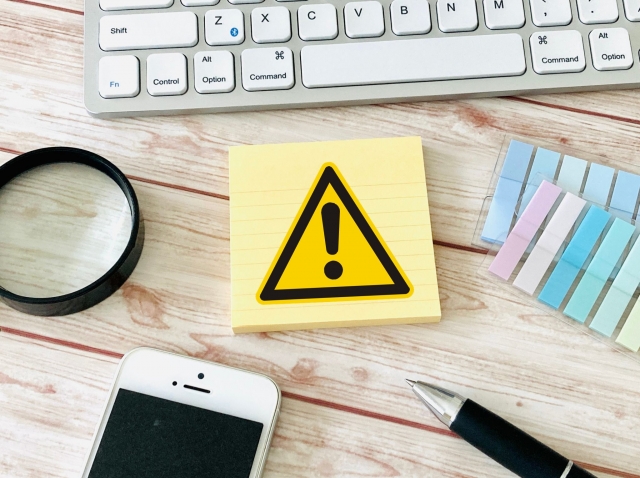
ポカミスが起こったら、その原因を解明し防止策を講じることが大切です。
ここではポカミスを防止するための手順を紹介します。
1. 情報収集
ポカミスが起こったら、まずはその状況を詳しく調べましょう。
情報収集する際はポカミスをした本人からヒアリングをするか、ポカミスの大きさによっては報告書を書かせます。
いつ、どこで、誰が、どのような状況でポカミスを起こしたのか、できるだけ詳しい情報を収集するのがポイントです。
本人以外にもポカミスの目撃者がいた場合には、その人たちからも情報を収集すると良いでしょう。
2. 原因解明
情報収集ができたら、ポカミスの原因を解明しましょう。
ポカミスの原因には思い込みや事実の誤認、注意力不足など様々な可能性が考えられます。
またミスの原因は、必ずしもポカミスを起こした本人にあるとは限りません。
上司の指示不足や作業環境の劣悪さが根本的な原因だったという事例もあるため、多角的な視点で解明を行ってください。
3. 対策の検討・実施
ポカミスの再発を防止するため、対策を検討し実施します。
ダブルチェックなど、すぐにでも実践できるポカミス対策もあります。
一方で作業員の怪我など深刻的なポカミスに対しては、抜本的な対策を行うことが不可欠です。
作業環境の改善など大規模な改革が必要な場合には、社内での会議や場合によっては設備投資が必要となるでしょう。
4. 関係者への情報共有
ポカミスは誰にでも起こりうることなので、その内容はチーム内で共有し注意喚起を促すことが大切。
ポカミス集のようなものを作って、そこにポカミスの内容や今後の対策についてまとめるのも良いアイデアです。
ミスはみんなが忘れたころにまた起こるものなので、定期的に過去のポカミスを見返すことで再発を防げるでしょう。
またマニュアルやルールを改定した際には、管理者がその都度周知を行ってください。
ポカミス防止の対策例
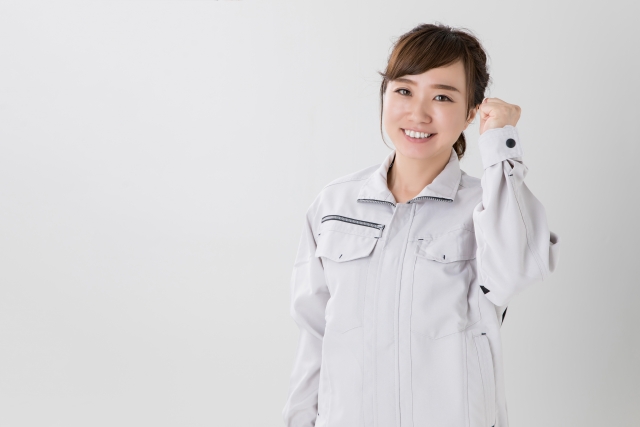
ポカミス防止のための対策を紹介します。
今すぐにできる対策から未然にポカミスを防ぐ方法まで、製造業にも役立つ対策をまとめました。
指差呼称
指差呼称とは対象を指さしながら、口に出して呼称することで、言い換えれば指差し確認のこと。
作業の際は対象をしっかりと目視し、指さしながらその名称や状態を呼称します。
呼称の仕方は、「○○よし!」が一般的。
指差呼称には注意力や緊張感を高める効果があるといわれていて、ポカミス対策としても有効です。
うっかりミスや見落としによるポカミスが多い人は、ぜひ実践してみてください。
フールプルーフ
フールプルーフとは、ヒューマンエラーを防止するための設計の仕方です。
例えば製造業の組立ラインでは、部品を正しい向きでなければ組み込めないように設計することがあります。
これは不良品を減らすためのフールプルーフの事例です。
フールプルーフを取り入れることで、単純なうっかりミスから重大な事故まで多くの問題に対応できます。
チェックリストの活用
チェックリストは作業の各工程を明確にし、漏れや誤りを未然に防ぎます。
見落としがちな項目は、太字やマーカーなどで強調しておくと良いでしょう。
文字が多いと読むのに時間が掛かるため、チェックリストはできるだけシンプルにまとめることがポイントです。
指差呼称と組み合わせて行えば、ポカミスが起こる確率をより下げることができます。
KY活動の実施
KY活動とは言い換えれば「危険予知活動」のことで、事故やミスを未然に防ぐための活動です。
活動の目的は作業に当たる全員がそのリスクを周知し、安全な職場環境の維持に貢献すること。
実施する際には、今後起こりうるポカミスを洗い出しその対策を検討します。
定期的な実施によりチームの安全意識が高まり、ポカミスの発生率の低下が期待できます。
マニュアル作成・研修体制の拡充
ポカミスを防止するためには、マニュアルの作成と研修体制の拡充が効果的です。
マニュアルには単に情報を羅列するだけでなく、わかりやすく見出しや図、目次も盛り込みましょう。
マニュアルがあれば研修もスムーズに進み、作業でわからないことを確認したい時にも便利です。
従業員一人ひとりが自信を持って業務に取り組めるよう、社員教育には注力しましょう。
作業環境や設備の見直し
作業環境や設備を見直すことで、ポカミスを防止するだけでなく作業効率を高める方法としても効果的。
例えば作業スペースの整理整頓を徹底することで、必要な道具をすぐに見つけられるようになり作業効率が向上します。
また設備のメンテナンスを定期的に行うことで、故障が起こりにくい状態を保つことも大切です。
設備の見直しはコストが掛かりますが、それによりポカミスを減らすことができれば企業にとってはメリットとなるでしょう。
まとめ
今回はポカミスの定義や事例、方法について解説しました。
ポカミスとはケアレスミスや凡ミスとも言い換えられる、人に起因するミスのこと。
ポカミスによって大きな損失や事故につながることもあります。
指差呼称やフールプルーフなど、適切な対策を講じることでその発生率を下げることができます。
ポカミスに悩んでいる人は、本記事に掲載したポカミス防止策をぜひ実践してみてください。