製造業における課題の一つが、品質、コスト、納期の優先順位の付け方です。
コストを優先すると品質が落ちたり、品質を上げると価格が上がったり、どうバランスを取るべきなのか悩む人は多いでしょう。
そういった問題に着目した考え方が、QCDです。
今回はQCDの意味や、生産管理においてQCDがどのように役立つのか詳しく解説します。
生産管理にQCDのフレームワークを活用したい人は参考にしてください。
この記事を書いた人:受発注ライフ編集部
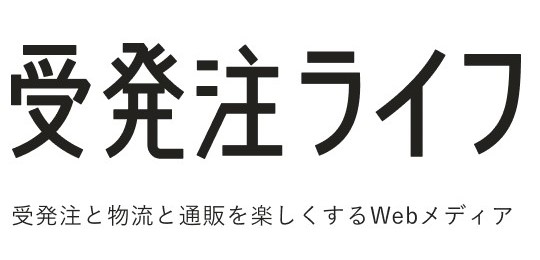
『受発注ライフ』は、2024年3月22日に誕生した、株式会社カンナートのWebメディアです。
株式会社カンナートは西新宿にある創業20年目のシステム開発会社です。
このメディアでは、受発注業務や物流、通販にお困りごとのある方々に向けて、 業務改善のアイデアや業界の新しい動向などを発信していきます。
QCDのフレームワークとは?
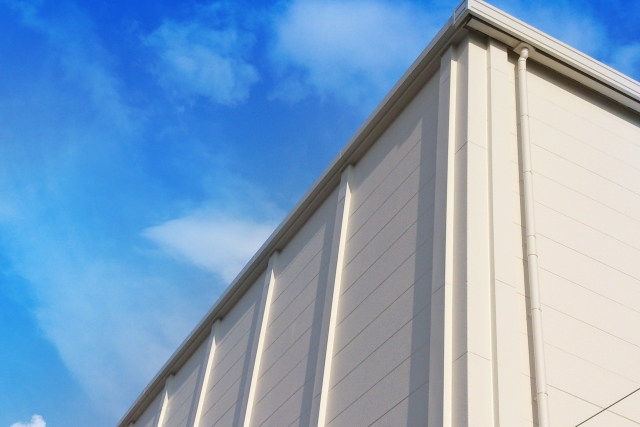
QCDのフレームワークとは、Quality (品質)、Cost (コスト)、Delivery (納期)の3要素を重視する考え方です。
これらの要素は相互に関連し影響を及ぼします。
Quality (品質)
QCDのQとはQuality (品質)。
製品やサービスの質を指し、QCDにおいては最も優先順位の高い要素です。
高品質な製品を作ることで顧客満足度が高まり、競合と差別化する上で大きな武器になります。
安定的に高品質の製品を作れば、製品そのものに対する評価だけでなく、ブランド力や企業に対する社会的信頼度も高まるでしょう。
Cost (コスト)
QCDのCとはCost (コスト)です。
製造業においては、原材料や人件費、設備費用、土地代、送料など様々なコストが発生します。
企業の利益を最大化するためには、無駄なコストをできるだけ減らすことが重要です。
しかしコストを抑えすぎると、品質や安全性、労働環境などが著しく悪化する恐れがあります。
どのコストを抑えどこは削るべきではないのか、適切に見極めることが大切です。
Delivery (納期)
QCDのDはDelivery (納期)です。
納期とは、製品やサービスが顧客に届く日のことを意味します。
納期を守ることは、顧客との信頼関係を保つうえで書かせません。
しかし無理に納期に合わせようとすると、作業が雑になり品質が低下することも。
納期を守りながら品質やコストのバランスを保つためには、無理のない生産計画を立てることが重要です。
QCDに類似する概念、派生語
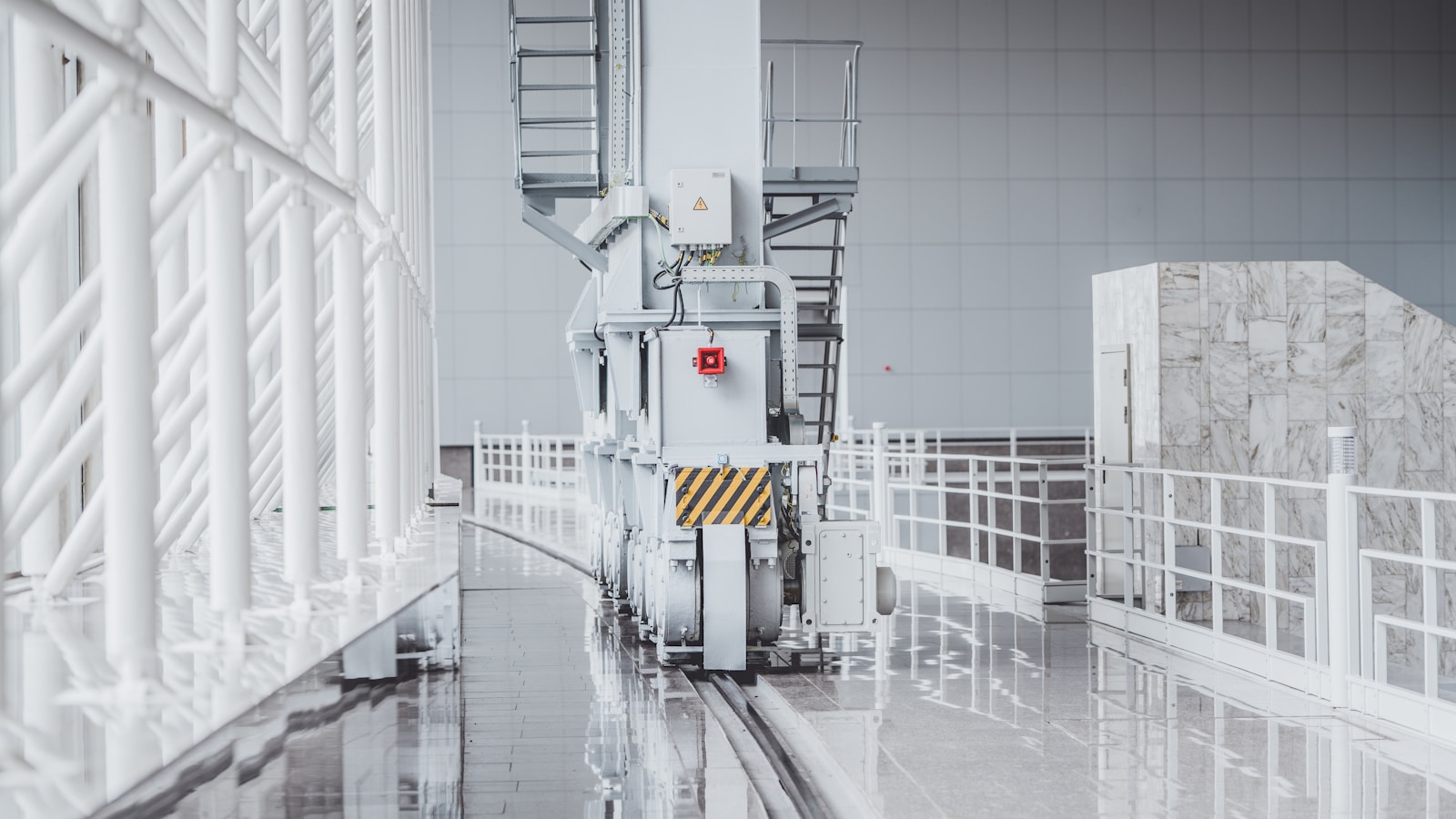
QCDに類似する概念や派生語がいくつかあります。
どれも生産管理に役立つフレームワークなので、QCDと併せて意味を知っておきましょう。
QCDS、QCDSE
QCDSはQCDに安全性(Safety)を加えたフレームワークで、安全性も考慮しましょうという考え方です。
安全性に対する対策としては、従業員への安全教育や作業環境の改善が行われます。
さらにQCDSEには環境(Environment)も加わり、環境への負荷軽減も重視されます。
PQCDS、PQCDSME
PQCDS、PQCDSMEのPは品種(Products)のこと。
ここでいう品種とは顧客が望む品物のことで、PQCDSは多品種少量生産を目指すフレームワークを意味します。
さらにPQCDSMEのMは士気(Morale)のことで、顧客だけでなく従業員にも視点を向けた考え方です。
生産管理におけるQCDのメリット
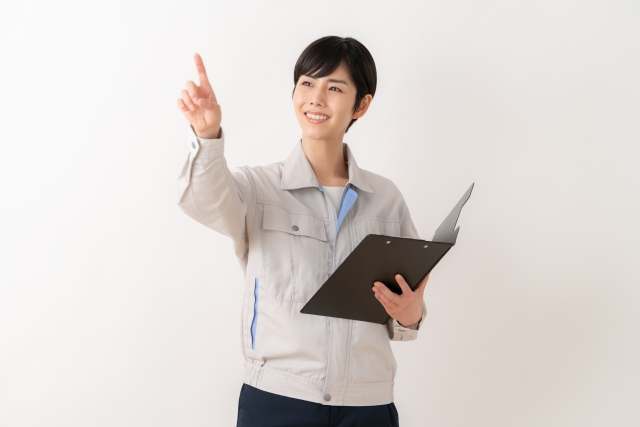
生産管理におけるQCD改善のメリットは、顧客満足度の向上や競合との差別化など様々です。
QCD向上に向けて対策を取ることで、組織の健全化に繋がることもあります。
顧客満足度の向上
QCD改善により得られる最大のメリットは、顧客満足度の向上に繋がることでしょう。
高品質で手頃でかつ短い納期で届く製品は、顧客にとって魅力的です。
顧客満足度が向上すれば、リピート客が増えるだけでなく、良い口コミが新規顧客も呼び寄せます。
企業が長期的に成長するためには、顧客満足度向上に向けた努力が欠かせません。
コスト削減、利益率アップ
QCD改善により、生産コストを下げて利益率を上げることができます。
ここで大切なのが、できるだけ品質を下げずにコストを抑えること。
設備を見直したり、無駄な作業プロセスを減らしたりすることで、品質を維持したままコストを削減するのが理想的です。
結果的に製品の価格を下げることができれば、競合との差別化にも繋がります。
業務の最適化
QCD改善のプロセスでは、品質向上、コスト削減、納期短縮の3つを実現するための対策が必要となります。
例えばシステムやAIの導入、作業手順の見直し、人員の再配置など、何かしらの対策を取ることになるでしょう。
結果的に業務の最適化が進み、無駄のない生産プロセスを確立することできます。
それに付随して、従業員にとって働きやすい職場の実現など、QCD以外の要素も改善する可能性があります。
競合との差別化
QCD改善が成功すれば、高品質な製品を適正な価格で、短期間のうちに消費者へ届けることが可能に。
品質、コスト、納期の3つのバランスが取れた製品は、多くの顧客層のニーズを掴むことができます。
そのため競合との競争に負けにくくなり、安定的に利益を上げることが可能となるでしょう。
その結果ブランド力が高まれば、企業全体の成長にも繋がります。
生産管理における、QCDの管理方法
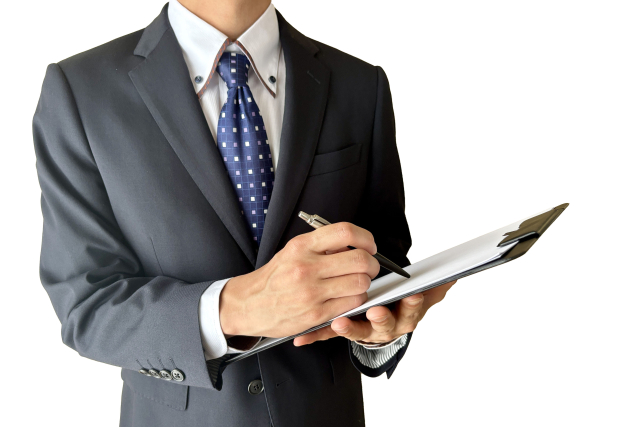
生産管理における、QCDの管理、評価方法を紹介します。
QCD改善のためには、3要素それぞれを定期的に評価し管理方法を見直すことが大切です。
品質の管理・評価方法
品質管理のうえでは、合格、不合格の基準を明確に設定することが重要です。
不良品や欠陥のある製品を見逃さないための、適切な評価方法を設けましょう。
また顧客からの要望やクレームを品質向上に反映させることで、顧客満足度の向上を期待できます。
品質の評価方法としては、品質検査、クレーム数や返品率の推移の確認などを行うのが一般的です。
コストの管理・評価方法
コスト管理では、人件費や材料費、設備費などの管理が必要です。
品質や安全性は担保しながら、非効率なプロセスなど無駄なコストは抑えていきましょう。
コスト管理の評価方法には、原価計算や予算と実績を比較する差異分析、コストの内訳を詳細に調査する方法などがあります。
また損益の計算が簡単に行える、原価管理システムの活用もおすすめです。
納期の管理・評価方法
納期遅延を防ぐためには、生産計画を立てることが重要です。
計画を立てる際は、各工数に必要な時間を把握したうえで、製品の製造、出荷にかかる時間を見積もりましょう。
生産段階で遅延が生じた場合にはその都度計画を立て直すことで、納期遅延を防ぐことができます。
納期の評価方法としては、納期を守った回数を総注文回数で割り、その割合を算出する方法があります。
QCDの優先順位の付け方
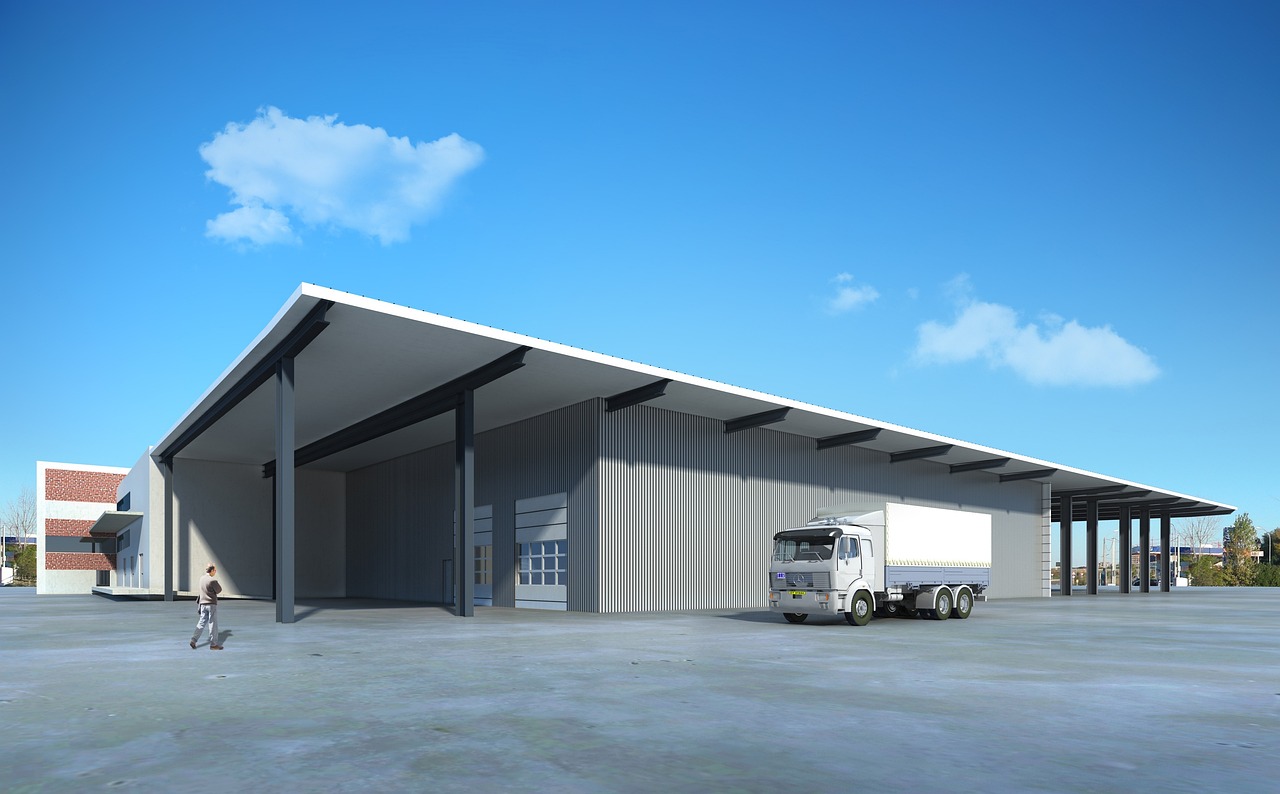
QCDのフレームワークを活用する際には、優先順位を決めたうえで3要素をバランスよく改善することが大切です。
品質が最重要
QCDの優先順位においては、品質が最優先されるべきです。
品質が優れていなければ、どんなにコストが低く納期が迅速であっても、顧客の満足を得ることはできません。
また品質の低下はリコールや保証クレームなど問題に繋がりかねず、企業の評判にも悪影響を及ぼす可能性もあります。
そのため、品質はコストや納期以上に重要な要素です。
コスト・納期は品質とバランスを取る
コストと納期の優先順位は、品質とのバランスや需要、競合の状況などを踏まえて総合的に判断すると良いでしょう。
また「納期は急がないからできるだけコストを抑えたい」など顧客のニーズが分かっているなら、それに応じて優先順位を決める方法もあります。
コスト、納期どちらを優先した場合でも、品質低下、作業者の負担増加などのリスクがあるため、QCDの全体のバランスを取ることが重要です。
QCDの改善方法
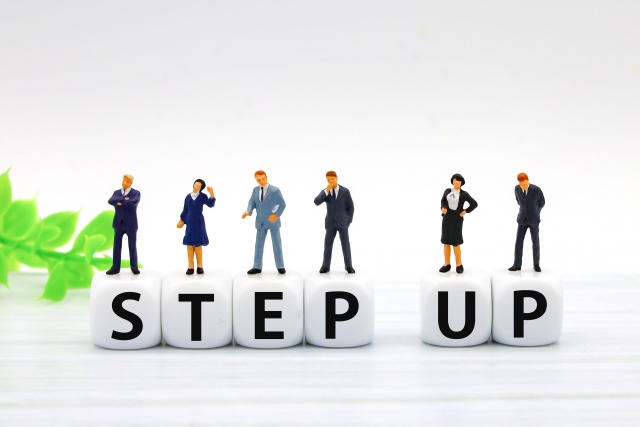
QCDの改善により、生産管理業務全体の最適化が可能です。
PDCAサイクルに沿って、一つずつ着実に課題を解決していきましょう。
1. 現状把握
QCD改善のためには、まず現状把握が不可欠です。
不良品の増加や納期遅延、原材料の価格高騰など、品質、コスト、納期に関して自社が抱える問題を洗い出してみましょう。
経営陣だけでなく現場作業員にもヒアリングしたほうが、より多くの問題が浮かび上がるでしょう。
また顧客からのフィードバックやクレームも参考にすることで、QCDのバランスを調整するうえでのヒントが見つかるかもしれません。
2. 改善策を検討、実施
次に、課題に対する改善策を検討しましょう。
課題が複数ある場合は、QCDのバランスを考慮して優先順位の高い課題から取り組むと良いでしょう。
検討の段階で具体的な改善方法や目標、評価方法まで設定しておくと、後々の効果検証がしやすくなります。
実施後は、現場で改善策が適切に運用されているかもチェックしましょう。
3. 効果検証
改善策が課題解決に繋がっているか、効果検証を行います。
効果はすぐに表れないこともあるため、1週間おき、1ヶ月おきなど定期的に検証すると良いでしょう。
また歩留まり率や製造原価、リードタイムなど、可能な限り定量的な指標に基づいて検証することが大切です。
検証の結果、効果が確認できなかった場合には、もう一度改善策を検討しPDCAサイクルを回しましょう。
まとめ
今回はQCDのフレームワークの意味や優先順位の付け方、評価方法などについて解説しました。
QCDとは品質、コスト、納期それぞれを重視する生産管理の考え方を意味します。
1つの要素だけを優先すると他の要素にマイナスの影響が及ぶことがあるため、QCDはバランスよく改善することが重要です。
品質を最優先に考え、コスト、納期の優先順位は需要や顧客の要望などを踏まえて決めてください。